Overcoming Label Material Supply Challenges
What happens when the material you use for an essential process is unavailable because of supply chain issues? Does it create disruptions that impact efficiencies, reliability and even revenues? Not if you take preventive steps to ensure an ongoing source of supply.
Executive Summary
A leading healthcare organization specializing in clinical diagnostics uses dozens of labels to facilitate various internal and customer-facing processes. With both domestic and international locations that serve doctors, hospitals, pharmaceutical companies, and more, the labels help them improve efficiencies, track data and provide their clients with the information they need. In addition, a few applications have exacting technical requirements which limits the type of materials that work properly. Plus, without this material or a viable alternative, the only option is to revert to a manual process which is inefficient, more costly and error-prone.
Exacting Requirements
The exacting standards required for the application added further complexities. First, both text and a barcode are printed on each label using a thermal transfer printer. Once printed, the labels are then applied to the substrate and subjected to harsh chemicals and stains. Throughout this treatment, the text and barcode must remain crisp and clear so the information is readable and the barcode scans successfully.
Supply Chain Disruptions
With label material suppliers located throughout the world, and certain coatings and chemicals only available outside the U.S., some materials draw from offshore locations. That was the case for this application. In normal times, that's not an issue. But, when you mix in COVID plant closures that delayed production, a weeks-long cargo ship backlog at U.S. ports and trucker shortages that slowed the final distribution of materials to their end destination, it creates a problem.
A Collaborative Solution
Fortunately, the healthcare organization leveraged their relationship with UAL/RRD which provided them with:
- Extensive experience in developing solutions for challenging healthcare applications
- Access to a technical team with unmatched knowledge of label materials
- Established relationships with numerous potential material sources
- A thorough and effective evaluation and testing process
Having worked collaboratively in developing the initial solution and with an in-depth knowledge of the process, the UAL/RRD team went to work. After extensive research narrowed the potential alternatives, supplier interviews followed which led to identifying a promising source.
What We Discovered
Unlike the thermal transfer material currently used, the alternative option used direct thermal technology. This required additional testing to ensure the material worked effectively from manufacturing through the end use of the product. Starting with an initial test quantity, the UAL/RRD technical services team ran the material through a variety of manufacturing steps, including printing and finishing, to ensure specifications, like the text and barcode clarity and die cutting, were met. Once those standards were achieved, they shipped a small quantity of the finished product to the customer for additional testing.
At the customer site, the onsite testing covered two important issues. First, it had to withstand the harsh conditions and perform properly in the end use application. Next, because this was a direct thermal material, switching from thermal transfer to direct thermal had to be quick and painless.
Both objectives were quickly achieved. The customer approved the material and UAL/RRD rapidly manufactured and shipped the label to the end use locations.
Summary
The new material provided the healthcare organization with a viable alternative allowing them to maintain an ongoing supply of labels and preserve the effectiveness and efficiency of this highly specialized operation.
UAL/RRD's more than 60 years of label experience goes beyond manufacturing to include the technical knowledge and supplier relationships that are essential during these times of supply chain constraints. Our team provides ongoing assistance to customers to not only ensure product availability but to offer continuous improvement and cost savings options. Contact us to learn more.
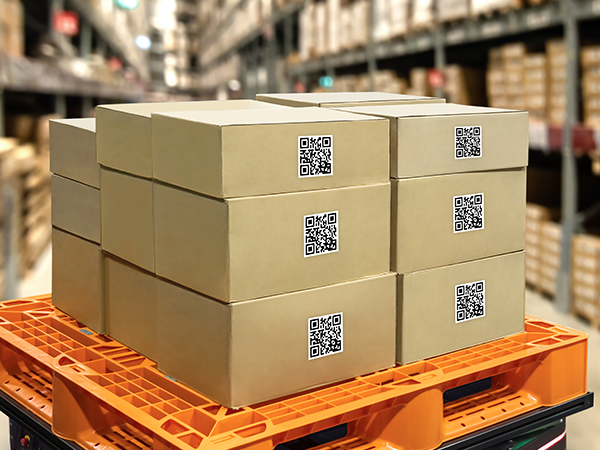