Frequently Asked Questions About Labels
Where are your labels manufactured?
We manufacture our labels in the USA and ship most of our labels from St. Charles, IL
What is your relationship to RRD?
United Ad Label is a brand of RRD, the world’s premier provider of print and related services. The RRD suite of products and services allow us to be a single-source supplier for all your healthcare communication needs.
Do your blood labels meet FDA material guideline CFR 21, Sec 175.105?
Yes, our blood labels meet this requirement.
What is the difference between Infrared Direct Thermal (IR) and Regular Direct Thermal labels?
Infrared direct thermal materials contain a special coating that is capable of being scanned with an infrared light source. If you are using an infrared scanner, you will need to use infrared materials, which also tend to scan better in conditions where blood and dirt might interfere with reading the barcode.
How are your stock labels packaged?
95% of our non-thermal stock labels come in convenient dispenser boxes that protect them from dirt and damage. Our direct thermal rolls are placed in black bags to protect them from light and promote maximum shelf life.
What are self-laminating labels?
Self-laminating labels feature an attached clear film strip on top of each label that you apply after writing your information on the label. This film protects the label from moisture, chemicals and also prevents tampering of written data once applied. Many of our equipment labels are available with this feature, or you can request any label to be made custom self-laminated.
What guidelines do you follow for your sterile labels?
Our gamma sterilized labels follow FDA guidelines for sterility and the sterilization process is validated annually to provide an SAL (Sterility Assurance Level) of 10-6. An annual audit of the validation process verifies the product is in compliance with ISO 11137 and TIR 27, and the packaging is validated in accordance with AAMI guidelines.
What if my barcode labels aren’t scanning?
Check the scanner first. Make sure it is functioning properly. If you are using an Infrared Scanner, be sure that your direct thermal materials are Infrared. If you are printing your own barcodes, check that the font is correct and that you are printing 300 dpi or higher. If printing on the direct thermal printer and the bars are not crisp or look smudged, you may need to adjust your printer’s heat setting. If you are scanning in a highly lit environment try scanning so that the barcode is not facing straight up at the light but rather at an angle to minimize the amount of light interference, and scan 6-12 inches from the barcode.
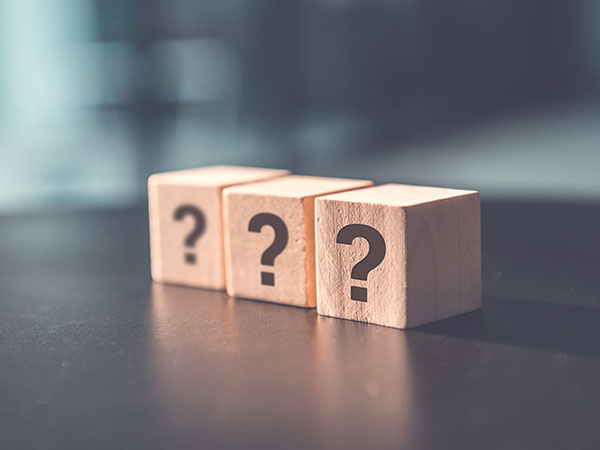